In their quest for innovation, FMCG manufacturers often overlook what’s already in their armoury, writes Adrian Swinburne

Head of Consumer
42 Technology
The constraints of existing high-value manufacturing assets, and the potentially prohibitive cost of investing in new ones, can often present a real barrier to product innovation. At best, it can stifle a company’s new product aspirations or even worse, prevent it from targeting new market opportunities because of the challenges in building a justifiable business case for additional capex.
Most conventional approaches for developing new products rarely consider the capabilities of existing manufacturing assets until late in the process, instead focusing on creating novel product concepts that address new market opportunities or consumer insights. Unfortunately, they’re often destined to fail later, when their impact on manufacturing is fully understood.
But, as 42 Technology has frequently demonstrated with FMCG sector clients, life doesn’t need to be like this; a manufacturer’s existing asset capabilities can become a highly potent catalyst for the innovation process rather than a barrier to it.
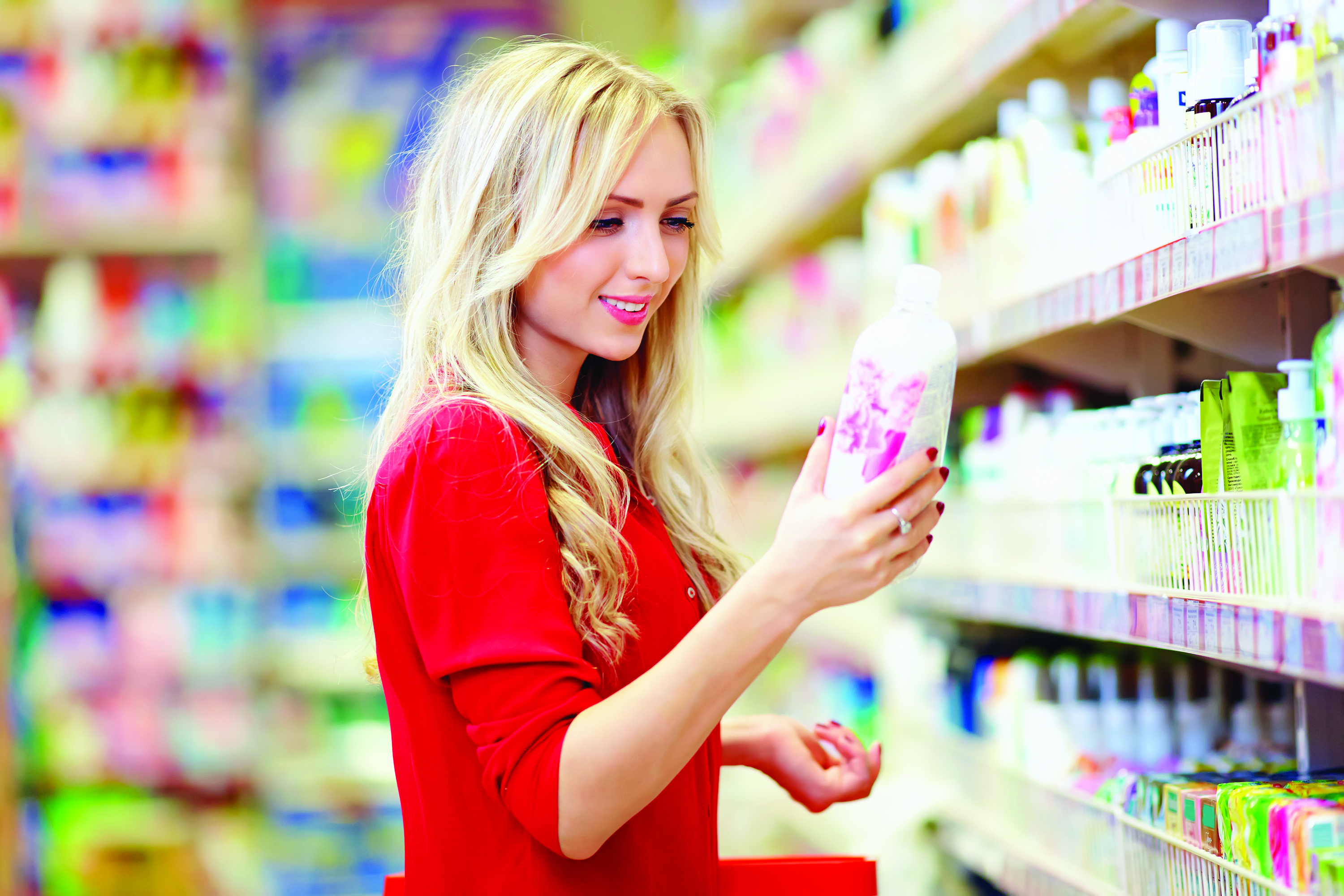
Constraining the innovation process
It’s now well acknowledged that creating structure within the innovation process can enhance the project team’s ability to create compelling ideas and also encourage even the perceived “non-creative” team members to make valuable contributions to the process.
But when it comes to ‘asset-constrained’ innovation projects, it’s essential to include the factory as part of the innovation environment from day one. In other words, to ensure the project scope includes an appropriate amount of time spent in the factory, understanding performance and capabilities of the equipment, working with key production staff, and exploring degrees of freedom and relative cost of change based on hypothetical process change scenarios.
It’s also vital to explore how those assets have evolved and most importantly, why changes were made. This can provide invaluable insight into true asset behaviour that may not necessarily be properly understood, and also identify where actual performance may differ substantially from management beliefs.
Creating manufacturable product ideas
When a company’s production assets are fully understood, the project team stands a greater chance of presenting new product ideas that resonate not just with the marketing team but also with engineers within the factory by demonstrating a genuine path towards product realisation.
For example: During one recent client project, the 42 Technology team was asked to conceive new premium products in an already successful personal care product category, specifically targeting a number of new consumer insights and unmet market needs. But rather than being given a free hand, the consultancy team was asked to limit new product concepts to those that could be manufactured using existing assets in a factory running below capacity.
As a direct result, the project was extended to consider the capabilities of and opportunities to modify existing equipment, and members of the consultancy team spent time within the factory to gain the best possible understanding of how those assets might be used.
By taking this approach the team identified and unlocked some unexpected capabilities that led to several, compelling new product concepts. And at the same time provided the FMCG brand owner with opportunities to realise greater value, as well as new efficiencies from existing production equipment.
In summary…
Although factoring in the capabilities of an FMCG brand’s existing manufacturing assets, or “Going to Gemba”, may not appear to be a revolutionary idea in itself, rarely does it take centre stage in the new product innovation process. But when properly considered, and when the appropriate skills are included within the project team from the start, this perceived barrier to NPD is often removed. And in many cases the additional capex associated with manufacturing new products or product variants can be significantly reduced through more palatable equipment modification rather than wholesale replacement.